Alcoa’s global refining research and development team won the ‘Australian Government Engineering Innovation Award’ for innovative technology that uses naturally occurring microorganisms to consume oxalate. The award was presented at the 2010 Australian Engineering Excellence Awards which took place in Canberra, Australia.
Oxalate forms in the alumina refining process as a result of organic material in bauxite ore. Organics enter the refinery liquor stream when bauxite is digested in caustic soda. This organic matter is broken down as part of the Bayer process with sodium oxalate being the predominant end product. This is an impurity that must be removed for optimum alumina production and quality. To prevent an eventual build up in the liquor stream, sodium oxalate is precipitated from the liquor stream as a crystalline material for disposal.
Sodium oxalate has few commercial uses and, until recently, must be either destroyed using a kiln or stored in secure impoundments. The conventional kiln process for sodium oxalate removal has a high capital cost, requires a flue gas RTO (regenerative thermal oxidiser) to control emissions and has a relatively high carbon footprint due to the fuel required.
In 1999, scientists at Alcoa’s Technology Delivery Group, based at Alcoa’s Kwinana refinery, began researching the use of naturally occurring bacteria to remove oxalate from the refining process. Over the next decade the group identified the specific alkali tolerant bacteria that could efficiently break down the impurity and developed an understanding of the optimum conditions under which the bacteria were the most effective. Through extensive testing and pilot plant work, an industrial scale process was developed.
The first full scale plant utilising this technology has now been installed and commissioned at Alcoa’s Kwinana refinery in Western Australia. The plant has exceeded all the initial performance specifications and is now operating well above its design capacity.
The new process, known as ‘continuous biological oxalate destruction’, is a cost effective and environmentally friendly solution to the oxalate challenge. The process is non thermal (maximum temperature of 40°C) with very low emission levels, emitting very little, if any, carbon dioxide. The greenhouse footprint of this process is around 40% less than the traditional kiln process, primarily due to a much lower fuel (energy) requirement. Although the biological breakdown of the organics generates carbon dioxide, this is quickly mineralised to inorganic carbonates and bicarbonates within the liquor stream passing through the process. The process has proven to be very efficient at destroying oxalate. The current system has sufficient capacity to treat both the refinery output of sodium oxalate together with the oxalate that was placed in temporary storage whilst the unit was being developed and commissioned.
Alcoa has since rolled out this technology to its Pinjarra refinery and at the PT Comfort Refinery in Texas, long-term, the process has the potential to consume all of the nearly 200 metric tonnes of oxalate removed each day by Alcoa refineries around the world, whilst also reducing energy usage.
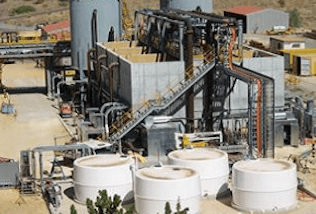
