However, the utilisation rate has been modest. Now, things are beginning to change. Industry-led efforts, supported by entrepreneurs, industry bodies, researchers, and universities, are looking closely at increasing utilisation rates.
There is still much work to be done, but the development and implementation of bauxite residue uses has never been stronger. It is estimated that between 2.5 million and 5 million tonnes is recycled annually, and used in the likes of cement production, road construction, refractories, soil amelioration, dyke construction and landfill covering.
Here are some of its uses:
The iron and aluminium found in bauxite residue provide valuable additions to the production of Portland cement at a low cost. Between 1 million and 1.5 million tonnes of bauxite residue are currently used annually in the production of clinker, which is critical to cement production. Used on an industrial scale across China, Russia, India, and Europe, evidence from these plants demonstrates that bauxite residue can successfully be used in cement clinker manufacture.
Potentially the largest use of bauxite residue in cement is in supplementary cementitious materials. Numerous groups have undertaken considerable work in this area, and opportunities for bauxite residue as a filler in blended cements have been explored. Some studies have shown that bauxite residue may successfully replace clinker in blended cements at dosages between 10-20%, while others have shown that 25-30% replacement is possible. This is could have a significant positive impact on the cement industry’s CO2 emissions.
There have been favourable recent studies on using bauxite residue in special cements, such as calcium sulfoaluminate cements. Encouragingly, these cements generate less CO2 during production than Portland cement. Not only that, but they possess high early strength characteristics, high ultimate strengths, and good dimensional stability. Despite this, there is currently no industrial usage of these cements. This may be because they require a higher alumina content than Portland cement, and bauxite is frequently used as the alumina source, which means their raw material cost is higher. However, using bauxite residue offers the opportunity to reduce this cost differential.
Using bauxite residue at refineries promotes a circular economy and encourages sustainability. It is used in road construction at sites, as well as in building levees, dyke walls, and impoundment areas. It is also used to reduce water ingress and promote vegetable growth when mixed with waste materials such as fly ash and capped with clay.
Bricks have been made with over 90% bauxite residue content when using a firing temperature of approximately 1000ºC.
Sandy and acidic soils can benefit greatly from the addition of bauxite residue. Extensive studies in Australia have found that it improved water retention and nutrient utilisation ability. As well as that, an increase in ammonium and phosphorus retention behaviours means that the use of fertilisers can be reduced.
When dewatered, the low permeability of bauxite residue is effective for capping landfills, particularly at municipal sites. At one site near Marseille in France, the waste methane gas that evolves is collected under the Bauxaline® covering layer. Similar practices have been utilised in Louisiana, where pH-reduced bauxite residue is mixed with clay.
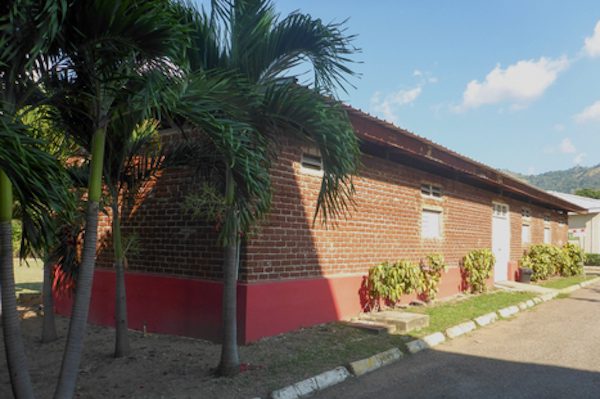
Applications for bauxite residue can broadly be broken down into five categories:
Products: It can be used as a major component in manufacturing other products, such as cement.
Construction: It is used as a component in buildings and construction.
Properties: Due to its low permeability and phosphorus-absorbing characteristics, it is used for specific properties, including soil amelioration or landfill capping.
Recovery of specific components: These include iron, aluminium, titanium, lanthanides, scandium, yttrium, and gallium.
Conversion to useful material: This is done by modifying the compounds present and for acid mine drainage and heavy metal absorption.