After liquid aluminium is syphoned off during the reduction process, it is transferred to furnaces for casting. Casting can refer to the production of moulded primary aluminium products that require further fabrication, as well as near-net shape products that require limited subsequent processing. Let’s explore both.
The molten aluminium syphoned from reduction pots is weighed, sampled, and analysed before it is poured into a holding furnace and heated to around 750°C.
To add corrosion resistance, strength, and other properties to the aluminium, alloying elements such as magnesium, silicon, and manganese are placed into the furnace. Metallurgical analysis verifies that the metal meets customer specifications before the molten, alloyed (or pure, unalloyed) aluminium is cast into products and prepared for transportation.
Other than liquid aluminium, the major products of an aluminium smelter include remelt ingots, billets, and slabs:
Remelt ingots
Made in various shapes and sizes, they are used as inputs to casting processes, where they are remelted before potentially being further alloyed and cast into near-net shape products. High-purity ingots can also be produced for specialist applications in the electronics and aerospace industries.
Billets
Log-shaped, they are used to produce extrusions for use in construction and transportation, as well as forging purposes in automotive industries.
Slabs
Cuboid-shaped, these ingots are the input to the rolling process.
Aluminium castings have the advantage of being produced to near-net shape, maximising the yield and minimising further machining. The transport industry consumes around 70% of aluminium castings, with machinery and construction applications making up the remaining 30%.
There are several casting methods:
Pressure die casting
This is particularly suited to producing large quantities of relatively small parts, up to around 5kg in weight.
Gravity die casting & permanent mould casting
Permanent mould castings are suited to high production runs. They are typically larger than pressure die castings; the maximum weight of these castings is usually about 10kg. Permanent mould castings are gravity-fed with a relatively low pouring rate.
Sand casting
Moulds are formed by ramming sand onto a pattern, and the pattern is removed, leaving a cavity in the sand. While sand castings do not have the dimensional accuracy of other casting processes, they are flexible in the number of castings produced.
Shell mould casting
This produces finer surface finishes than sand casting and gives greater dimensional accuracy. Equipment and production costs are relatively high, and the size and complexity of the castings are limited.
Plaster casting
Plaster moulds have high reproducibility, which means castings can be made with fine detail and close tolerances. Although the costs for basic plaster casting equipment are low, the operating costs are high.
Investment casting
This produces components that require almost no further machining and is often used in the production of precision-engineered parts.
Centrifugal casting
There is a limitation on the shape and size of the castings available by this method. The casting cost is high, but the integrity of the castings comes closer to that of wrought products and equates well with permanent mould castings.
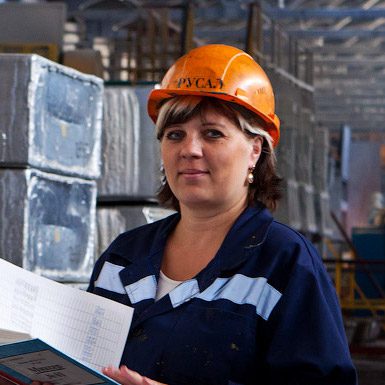
Casthouse Controller
RUSAL’s Volgograd Aluminium Smelter
“Innovation – in our processes and in the alloys we produce – is what is leading the industry to grow in new markets and cutting edge applications.”